レクサスUX 300e
開発プロジェクト
トヨタ自動車九州が、初めて主体となり開発した新型車「レクサスUX」
その次なる展開は、レクサスブランド初のEV(電気自動車)仕様となる「レクサスUX
300e」の開発だった。
トヨタ自動車九州としても、レクサスブランドとしても初めての挑戦が幕を開けた。
MEMBER
-
技術統括部技術企画室
製品企画グループ内村 容基也
-
設計部 内装設計室
内装・コックピット設計グループ川原田 真実
-
設計部 電子設計室
ワイヤーハーネス設計グループ久保 泰朝
-
性能・生産SE部 生産SE室
塗装組立グループ
(部署はプロジェクト当時のもの)南 浩生
-
品質管理部 品質管理室
機能グループ塩山 大騎
-
調達部 設備調達室
車両設備調達グループ田原 啓太郎
-
工務部 生産管理室
部品管理グループ山田 信介
メンバーと担当業務
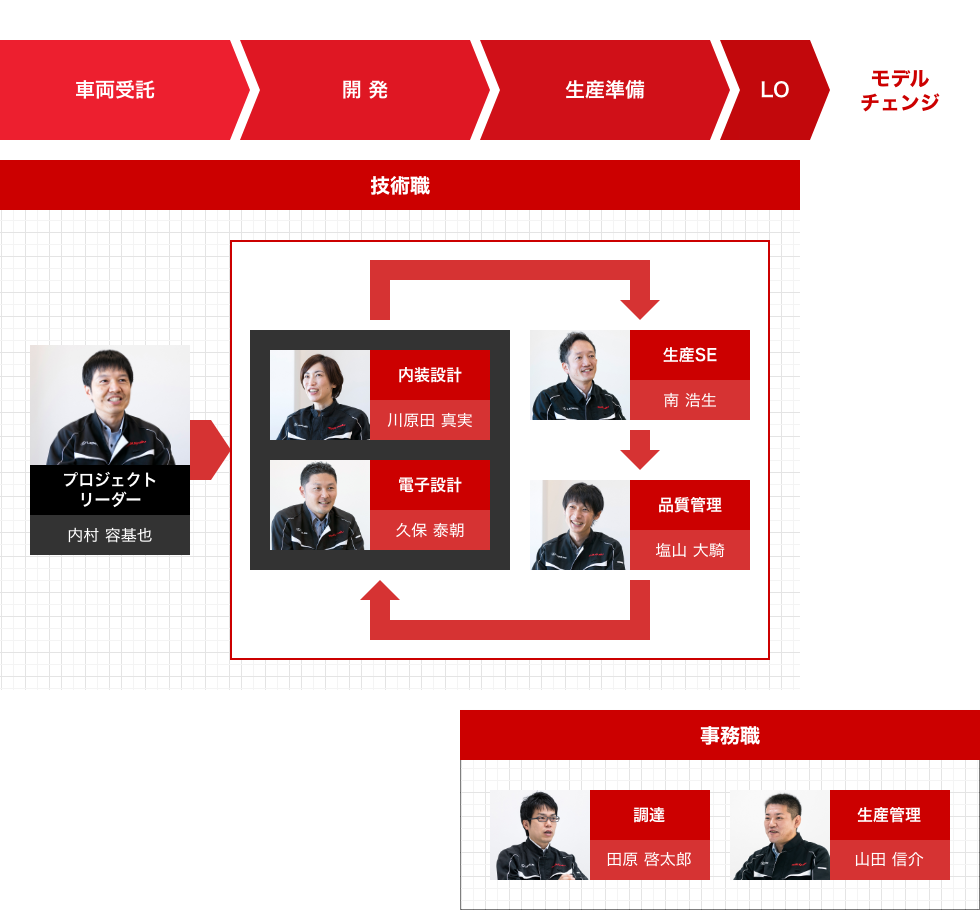
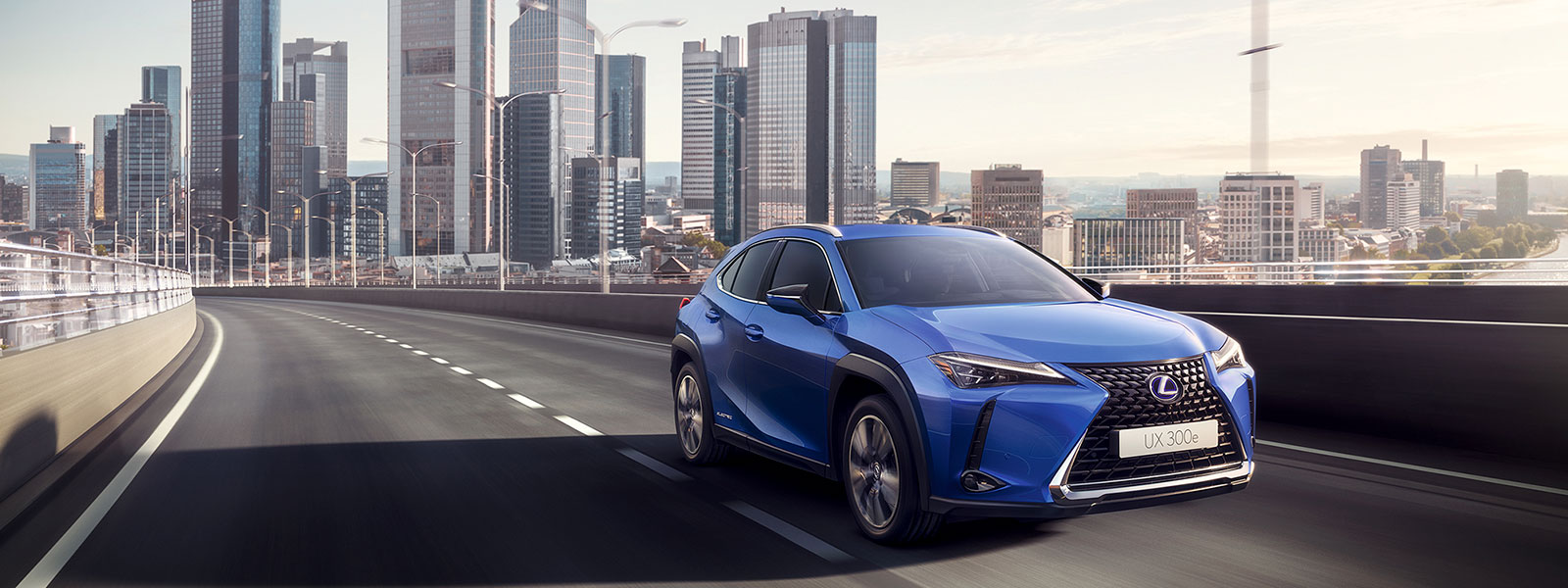
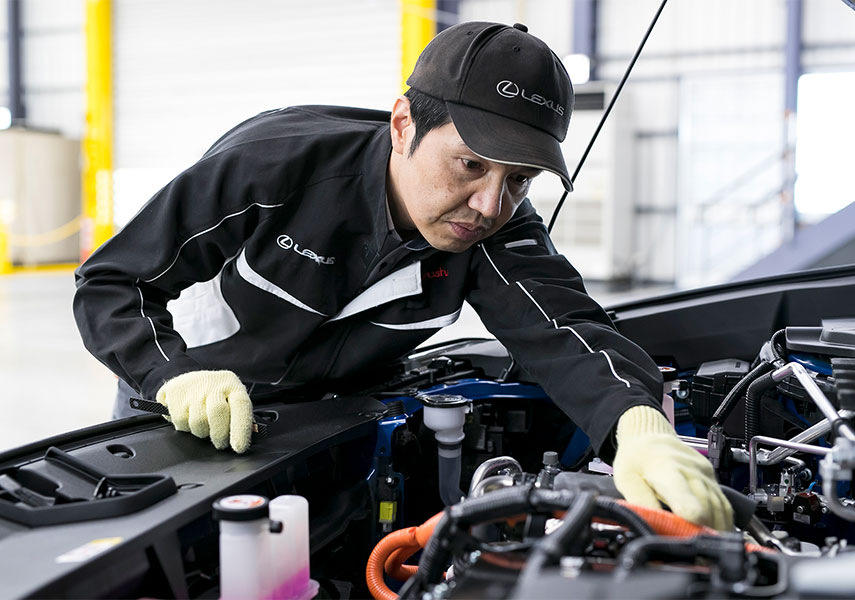
挑むのはレクサス初のEV開発
全員が手探りの状態からスタート
「約400kg! そんなに重いのか…」
UX
300eに搭載されるリチウムイオンンバッテリーの重さを初めて知った時、プロジェクトリーダーを務める内村容基也は衝撃を受け、「これは大変なプロジェクトになる」と腹をくくった。ベース車両となるUXをはじめ、数々の開発プロジェクトに参加してきた内村にとって、HV(ハイブリッド車)開発の経験こそあったものの、EVに携わるのはこれが初めて。HVの場合、バッテリーの重さは50㎏程度、後部座席の下に収まるくらいのサイズだが、EVとなると床下一面をリチウムイオンバッテリーが覆うことになる。これまでの知識や経験がどの程度役に立つのか、新たに何を学ばねばならないのか、暗中模索のスタートとなった。
内村だけではなく、プロジェクトメンバー全員にとってEVの開発は初めてのこと。それもそのはず、今回のUX 300eは、レクサス初のEVであり、さらにトヨタグループとしても2003年に生産を終了した「RAV4 EV」以来のEV開発となる。トヨタ自動車九州はおろか、トヨタグループとしてもチャレンジングなプロジェクトだったのだ。
困難な開発プロジェクトになることを覚悟しつつも、内村はレクサスらしさを維持することにこだわると心に決めた。走り始めから車を止めるまでの「すっきりと奥深い走り」。EVになったからといって、レクサスの真骨頂ともいえるシームレスな走りを追求する姿勢は決してぶらさない。そんな高い目標とは裏腹に、内村が最初に着手したのは「EVを知る」ということからだった。ガソリン車やHVとの違いについて、モーターやリチウムイオンバッテリーの構造についてなど、ゼロから学びを深める必要があったのだ。
プロジェクトメンバーの長く険しい戦いが始まった。
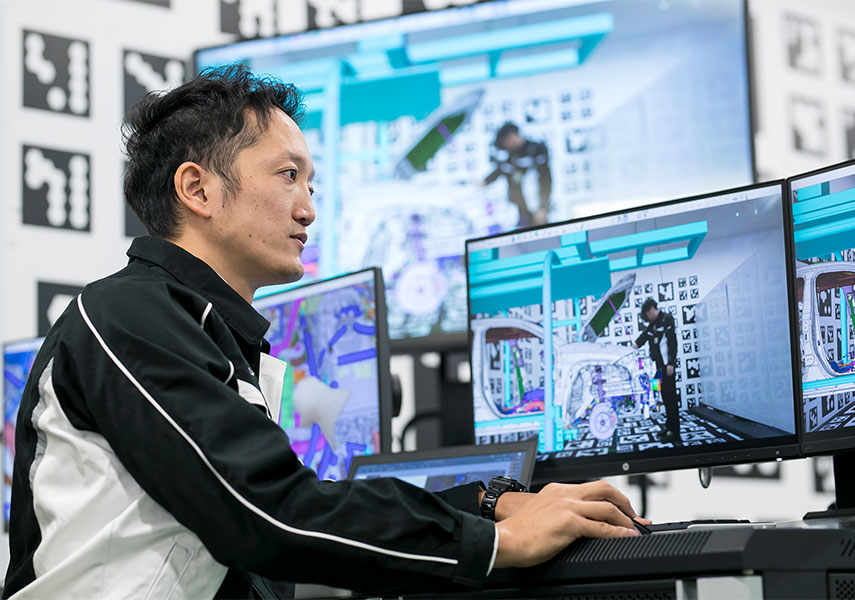
設備の大規模改造を回避した
起死回生の「組立ライン分岐案」
内村のほかにもう一人、プロジェクトの初期段階でリチウムイオンバッテリーの大きさに頭を抱えた人物がいた。当時、生産SE室でボデーに部品を組付けていく工程の検討を行っていた南浩生だ。大型のリチウムイオンバッテリーはUX 300eの航続距離を飛躍的に伸ばすための生命線だが、工場のラインで部品を組付ける際、その大きさゆえに生産設備とぶつかり、ラインを止めてしまう恐れがあった。車両を運ぶ搬送設備とバッテリーとの干渉をシミュレートすると、実に9種の設備のうち7種の改造が必要という絶望的な事実に直面。搬送設備を改造する場合、必要な費用や時間は膨大なものとなる。プロジェクト予算、開発日程に影響を及ぼしかねない重大な選択を、南は早々に迫られることになった。
「何とかしなければ…」、さまざまな解決策に思いを巡らせる中で南が参考にしたのは、2015年までトヨタ自動車九州で生産していた「レクサスIS C」の工程。組立ラインの最終工程から専用工程へと分岐させて、開閉式ルーフパネルを組付けていたのだ。同じように専用工程ラインを設けて最後にバッテリーを組付ければ、設備との干渉を回避できる。絶望の闇に光が差し込んだ瞬間だった。
光が見えたとはいえ、まだまだ課題は山積みの状態。バッテリー組付けの専用工程に必要な設備、車両、人の動線を工場内の限られたスペースで実現させる作業は困難を極めた。また、ラインを分けることで組立作業に無駄が発生し、生産性が落ちるデメリットも指摘された。いくつもの壁にぶつかりながらも南を奮い立たせたのは、レクサスが掲げる「二律双生」の精神。相反する価値を同時に叶えるという意味をもつこの造語によって、現在のレクサスブランドは創り上げられてきた。今回のプロジェクトにおいても南は二律双生を成立させ、大幅な設備の改造をすることなく、UX 300eの生産準備を完遂した。
「変えないように変えていく」
相反する課題に向き合う
設計チームにとって今回のプロジェクトの悩みの種となっていたのは、UXをベースにしたEVであるという点だった。新規車両の開発ではないので、UXとしての意匠(デザイン)を大きく変えることや、機能性、乗り心地などを妥協することは許されない。その一方で、EV化に伴う数々の変更点を成立させた設計にするという難しい課題が突き付けられた。
内装設計室・川原田真実は、インパネコンソールやフロアカーペット、ツールボックスの設計を担当した。川原田が関与する部分だけでも、リチウムイオンバッテリーを座席下に搭載することでフロアの高さや形状が変わる、充電ケーブルを収納するスペースがツールボックス内に必要で、かつ輸出先によって形状や長さが異なるなど、レイアウトの見直しが必要な箇所は多くあった。変えてはならない部分を守りつつ、EV仕様へと変えていく。まさに設計上の「二律双生」実現に奮闘していくことになった。
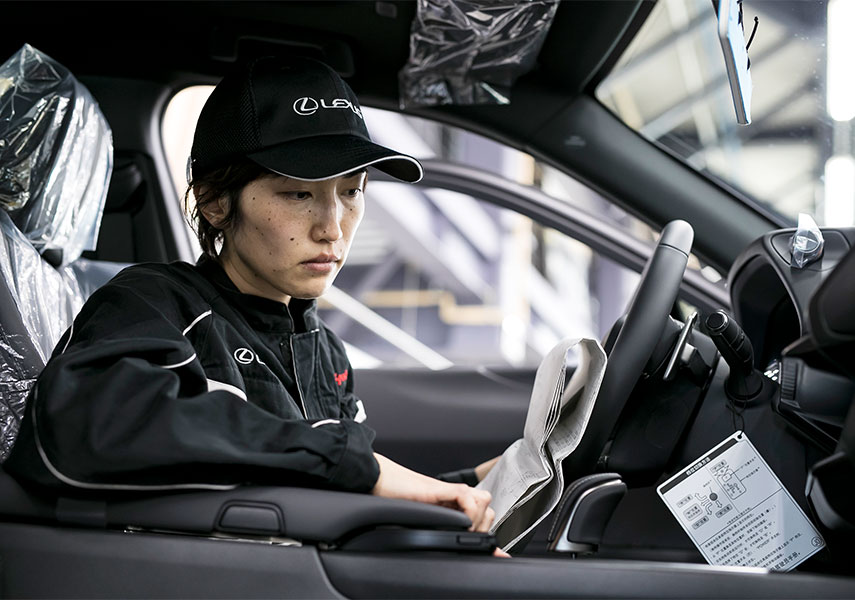
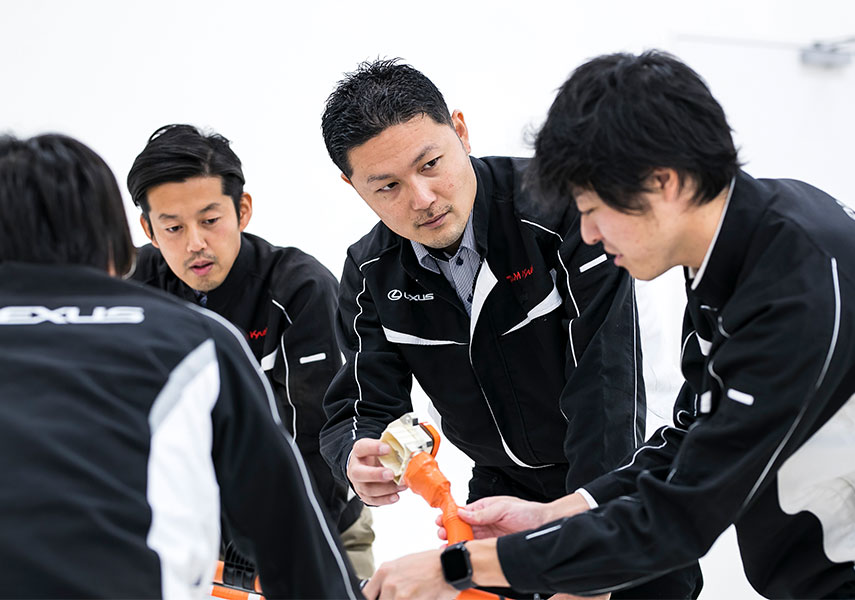
川原田と同じ設計部に所属し、車両の隅々に張り巡らされ電気系統すべてを司るワイヤーハーネスの設計を担当したのが、電子設計室の久保泰朝。久保にとって予想外だったのは、度重なる仕様の変更や追加だった。レクサス初のEVに対するニーズは高く、開発途中で輸出先が増えたり、仕様が追加されたりしたことに伴うものだが、開発日程を遅らせるわけにはいかない。短期間での柔軟な対応。これもまた「二律双生」へのチャレンジだった。
今回のプロジェクトの各所で直面する二律双生の実現において大きな効果を発揮したのが、「同席設計・同席評価」という初めての試み。従来のような、設計が終わってから生産技術担当者が組立工程を検討し、設計に問題があれば修正を依頼するという流れではなく、最初の段階から設計チームと生産技術チームが同席し、ラインでの組立のことまで踏まえた検討を重ねていった。その結果、課題の早期解決につながり、後からの設計変更は大幅に減少した。プロジェクトメンバーの多くが同じテクニカルセンター内で働き、何かあればすぐに集まれる距離の近さがあるというのは、トヨタ自動車九州ならではの大きな武器。開発から製造までがコンパクトにまとまっているからこそ、「同席設計・同席評価」をはじめとした密なコミュニケーションが可能となり、困難な「二律双生」の数々を叶えることへとつながっているのだ。
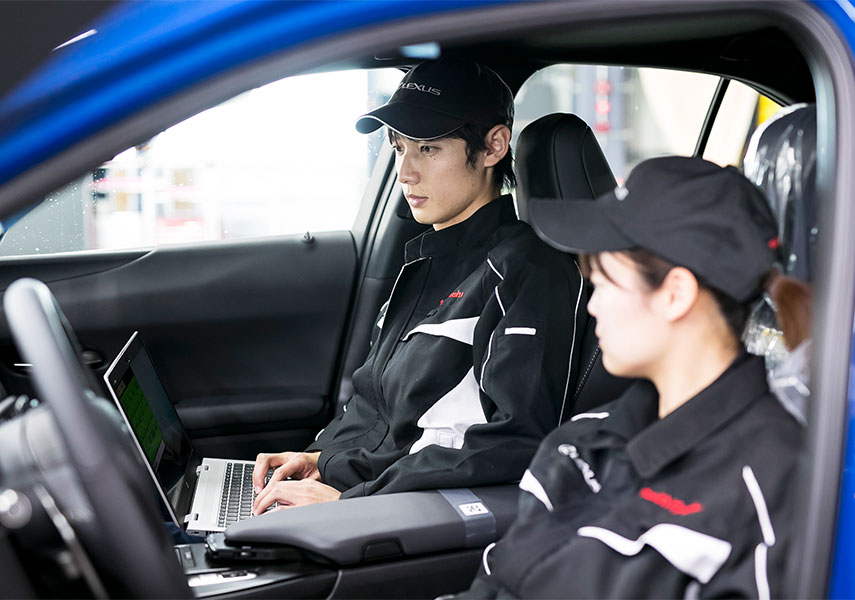
1日2,000km走行、コロナ禍の欠品
プライドをかけた
プロフェッショナルの奮闘
開発が終盤に差し掛かり、量産化に向けて品質の総仕上げが行われている頃、品質管理部の塩山大騎は、宮田工場内にあるテストコースでUX
300eの試作車を一心不乱に走らせていた。その距離、1日に約2,000㎞。東京、福岡間の往復に匹敵する途方もない長さである。ユーザーのさまざまなクルマの使い方をイメージし、バッテリーの充電度合いなど、あらゆるパターンを想定。走行中に不具合がないかを一つひとつ検証していく地道な作業を重ねていった。他にも中国のリチウムイオンバッテリー生産工場を視察するなどして、トヨタ自動車九州オリジナルのEV検査保証体制を考案。品質管理者としてのプライドが、塩山を駆り立てていた。
「レクサス初のEVという期待値の高さをひしひしと感じていました。我々は品質を司る部署なので、『絶対に不具合を出してはならない』という覚悟をもって、プロジェクトに臨みましたね」。
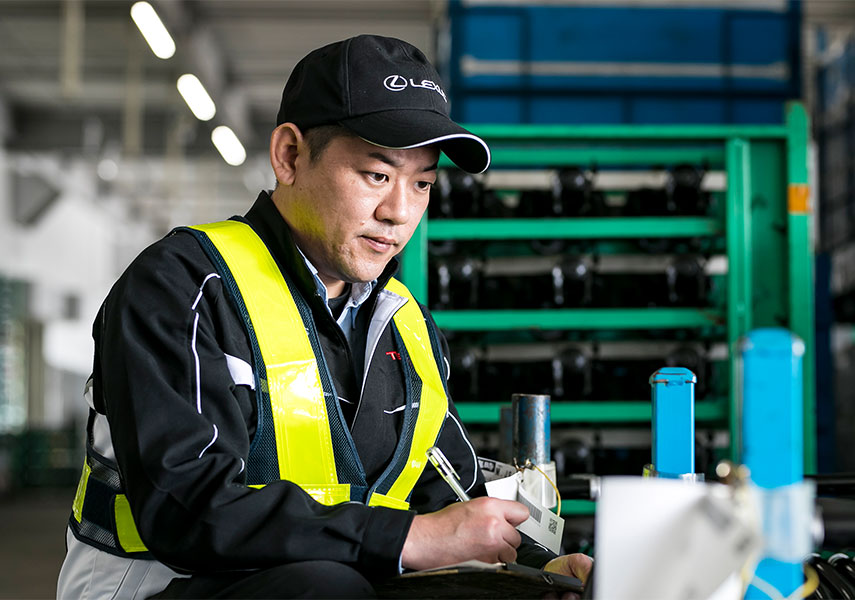
塩山がテストコースを駆け抜けていた同じ頃、生産管理室の山田信介は、世の中の様相を一変させた予期せぬトラブルと戦っていた。山田が担当しているのは、車両生産に必要となる部品の発注や在庫管理。その数は一つの車両で約4,000品目にも及ぶ。その部品の一部が、期日になっても工場に届かない。新型コロナウィルスの感染拡大によって、中国の部品生産工場が操業を停止したことが原因だった。トヨタ自動車九州でも、工場が稼働と停止を繰り返す状況の中、どの工程の、どの部品が、いつまでストックされているかを1点ずつ確認。プロジェクトリーダーの内村と連携して、ラインを動かす日程の変更、優先的に生産すべき部品の選定、代替品の検討などを進めていった。一部のテストで遅延が発生したものの、開発の全体的なスケジュールが遅れることなく量産化へといたった陰には、山田たちによる想像をはるかに超える努力があった。
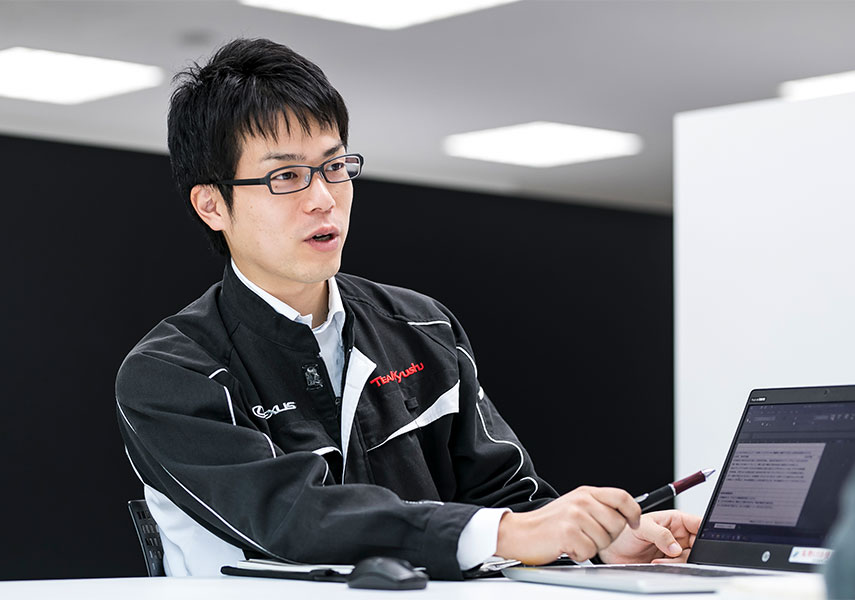
「自ら考え、行動する」
そして、次なるステージへ
いくつもの困難を乗り越え、UX 300eは2020年4月の中国を皮切りに、欧州、そして日本でも販売を開始した。EVの開発という新たな道を切り拓く過程では、先に紹介した「同席設計・同席評価」をはじめとするチャレンジングな取り組みがあり、そのいくつかは後続プロジェクトにおいて標準化されている。
デジタルツールを駆使した効率的な開発、生産準備態勢の確立もその一つ。VR(仮想現実)や AR(拡張現実)の先にあるMR(複合現実)デジタル検討システムが、UX 300eの開発で初めて導入された。工場での組付け作業を検討する際などに、仮想空間にリアルな人の手を入れて確認ができるため、まだ設備が完成していない段階から詳細なシミュレーションを行うことが可能。問題の早期発見、解決に大いに役立っている。
トヨタ自動車九州にはTEAM Kyushuというスローガンがある。仕入先を含めた、「九州のものづくりの力を結集して、世界中のお客様が求めるクルマを提供し続ける」という決意を表したメッセージだ。設備調達室で生産設備の仕入先選定、発注を行った田原啓太郎は、社内だけでなく仕入先と共に進化できたという点も、UX 300eのプロジェクトにおける大きな成果だと実感している。開発期間中、週に一度のペースで仕入先とのミーティングを実施。進捗状況や困り事、課題などを丁寧に洗い出していく試みが初めて行われた。製品評価の指標となるQCD(Quality、Cost、Delivery)すべてをレベルアップさせ、TEAM Kyushuとして仕入先と共に成長していくこの取り組みもまた、後続プロジェクトへと継承されている。
今回のプロジェクトでトヨタ自動車九州が得たもの。それは、一人ひとりが「自ら考え、行動する力」を養えたことだと、内村は総括する。前例のないプロジェクト、過去のノウハウが通用しない状況の中で、最高のクルマをお客様に届けるために自分がすべきことは何かを全員が考え、トライ&エラーを重ねながら行動した結果が、初めてのEV開発を成功へと導いたのだ。
ともに、九州から世界へ―。
トヨタ自動車九州は新たなステージへと着実に歩みを進めている。
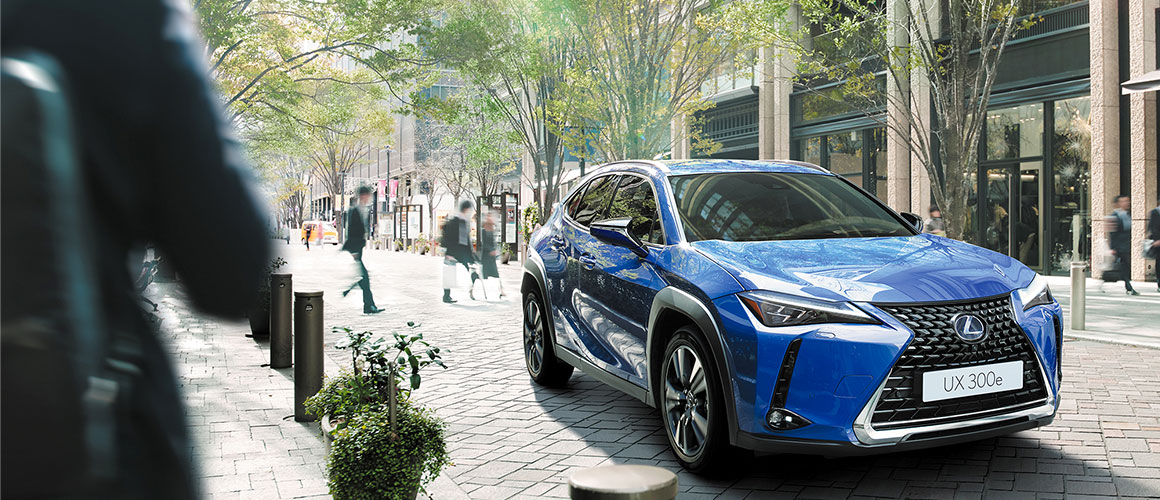